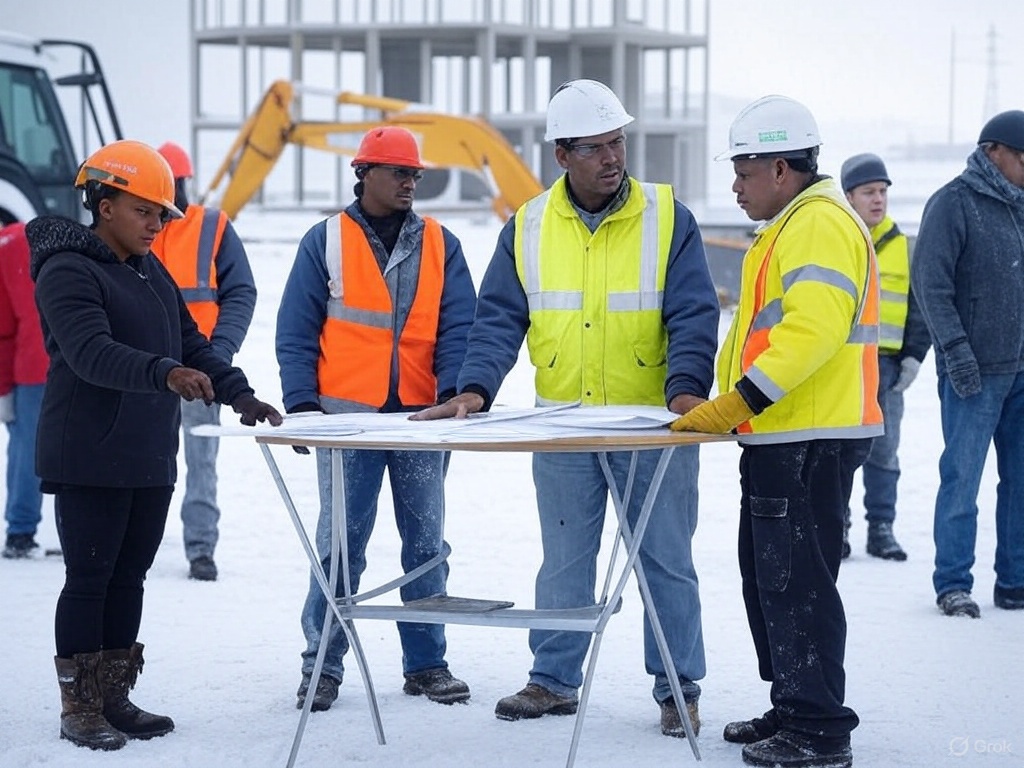
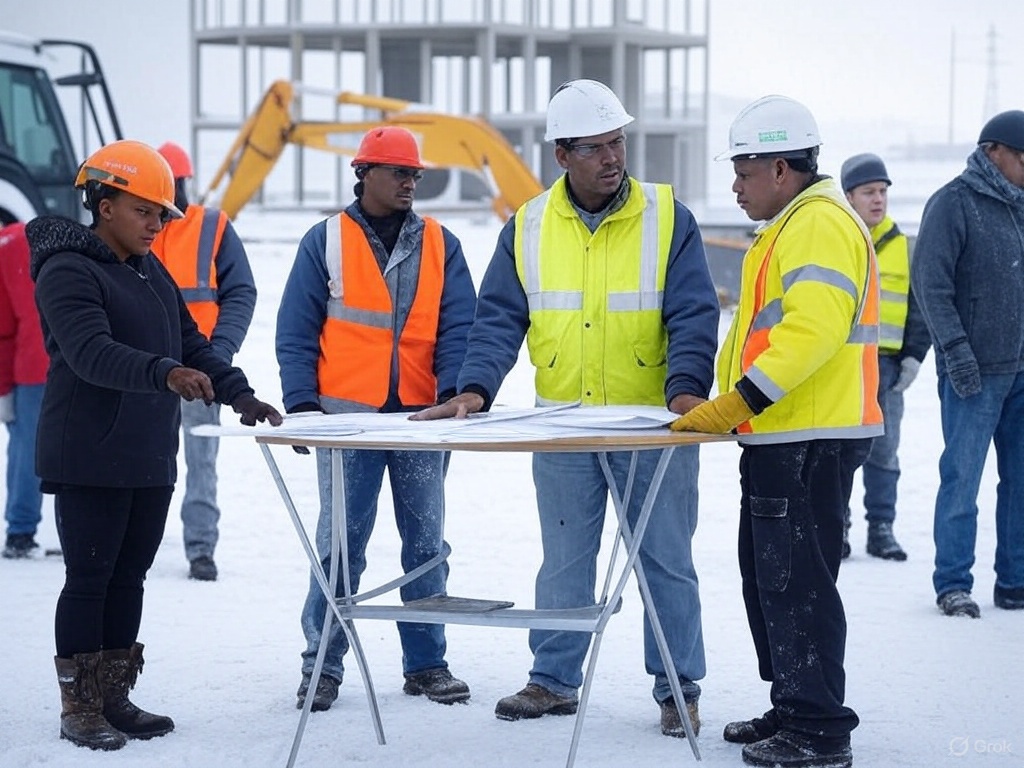
Winter presents unique challenges for construction projects, from safety hazards due to icy conditions to decreased productivity caused by cold temperatures. However, with proper planning and execution, construction can continue effectively throughout the winter months. Here are essential tips for maintaining safety and efficiency during cold weather construction:
1. Prioritize Safety
Warm Clothing and Gear: Ensure all workers are equipped with proper winter gear, including insulated boots, gloves, hats, and layered clothing to prevent hypothermia and frostbite.
Slip and Fall Prevention: Use de-icing materials on walkways, ramps, scaffolding, and work areas. Non-slip mats and shoe grips can also enhance traction on icy surfaces.
Regular Breaks: Schedule regular, short breaks in heated areas to allow workers to warm up, especially in extreme cold.
Emergency Preparedness: Have a clear emergency response plan that includes procedures for treating cold-related injuries and how to contact emergency services.
2. Efficient Site Management
Material and Equipment Protection: Store materials in a dry, covered area to prevent moisture damage. Use insulated blankets or covers for equipment to maintain optimal operating temperatures.
Work Schedule Adjustments: Consider adjusting work hours to take advantage of warmer daylight hours. Shorten shifts in extreme cold to reduce exposure.
Heated Enclosures: Use temporary, heated enclosures (tents) for tasks that require a warm environment, such as painting or finishing work.
3. Equipment Maintenance
Pre-Heating Equipment: Start machinery and equipment before use to warm up fluids and components, reducing the risk of breakdowns.
Regular Inspections: Conduct frequent inspections of machinery, tools, and equipment to ensure they are functioning properly in cold conditions.
Antifreeze and Lubricants: Use antifreeze for cooling systems and winter-grade lubricants for machinery to prevent freezing and ensure smooth operation.
4. Material Considerations
Cold-Weather Concrete: Follow proper procedures for placing and curing concrete in cold weather, including using accelerators, insulation, and heated water.
Adhesive and Sealant Limitations: Check the temperature ratings of adhesives, sealants, and paints to ensure they will set and cure correctly in cold conditions.
5. Communication and Coordination
Daily Briefings: Hold daily briefings to update workers on weather forecasts, site conditions, and any changes to the work plan.
Team Coordination: Encourage open communication among workers and supervisors to report any safety concerns or equipment issues promptly.
Resource Allocation: Allocate resources efficiently, anticipating potential delays due to weather. Keep extra materials, tools, and equipment on hand to minimize downtime.
6. Keep Morale High
Positive Environment: Foster a positive work environment to keep morale high during challenging winter conditions.
Recognition: Recognize and reward workers for their efforts in maintaining productivity and safety during adverse weather.
Training: Provide training on cold-weather safety protocols and efficient work practices to prepare workers for winter conditions.
By implementing these winter construction tips, project managers and construction workers can maintain safety, productivity, and morale throughout the cold season. Remember, thorough preparation, constant vigilance, and a proactive approach to challenges are key to successful winter construction.